Current Research Projects
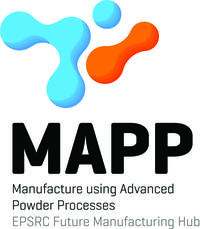
The group is a partner for one of the UK's Future Manufacturing Hubs. The UK's Engineering and Physical Sciences Research Council (EPSRC) is investing £10M in the Manufacture using Advanced Powder Processes (MAPP) Hub, led by the University of Sheffield and also involving the universities of Oxford, Leeds, Manchester and Imperial College London, 17 industry partners and six centres within the UK's High Value Manufacturing Catapult.
MAPP is focusing on developing new powder-based manufacturing processes that provide low energy, low cost and low waste manufacturing routes and products for UK industry. Our work in Oxford concerns novel uses of the field assisted sintering technique (FAST) for consolidating powder materials, and controlling the associated microstructural evolution in a variety of structural and functional materials.
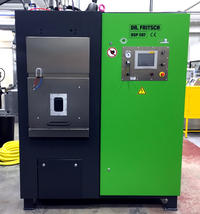
Right is our Dr Fritsch field assisted sintering technique (FAST) apparatus. FAST is a powder consolidation process in which a pulsed direct current is passed through a green powder compact and/or a graphite die under vacuum and uniaxial pressure. Joule heating in the die and/or the compact (depending on die arrangement and materials used) reduces consolidation times from many hours to a few minutes. FAST is similar to the Spark Plasma Sintering (SPS) process.
The FAST is being used to consolidate Fe, Cu and W based dispersion strengthened powders produced in-house for nuclear power applications, and solid-state electrolytes for batteries.
The group and a consortium of researchers from across the UK have been awarded approximately £12M for project Nextrode that is researching new ways of making the electrodes found in the 6 billion (and growing) Li ion batteries produced every year.
Today's Li-ion batteries use electrodes that are made using a "slurry casting" process in which the active materials are mixed in a wet slurry and coated onto thin metallic foils, then dried and compressed. For the anode, the active material is typically graphite (a form of carbon), while for the cathode it is usually a more complex Li-based oxide. The slurry casting process is highly effective for mass production, but has been developed through trial and error. When the active material or the electrode formulation is changed, the time-consuming trial and error optimisation of the manufacturing process and the electrode microstructure must start again. The process also has limited opportunities for more careful tailoring of the electrode structure, which recent lab-scale and simulation work is beginning to show could be effective in boosting battery power, energy density and/or lifetime. However, until now, no such manufacturing technologies have been available at anything like approaching the required scale and throughput.
"Nextrode is strengthening the scientific understanding of existing electrode manufacturing, which we can then apply to bring more flexibility to slurry casting in order to realise battery performance improvements at industrial scale. At the same time, we are developing a new generation of manufacturing approaches for 'smart' electrodes where the different electrode materials are arranged with greater precision and provide even greater performance benefits. This part of the work is focused at Oxford University, drawing on the expertise of our partners at Sheffield, Birmingham, Warwick, Southampton and UCL. We are also working with industrial partners who will help us apply our insights and ideas at industrial scale".
Studying crystallization using X-ray radiography and machine learning
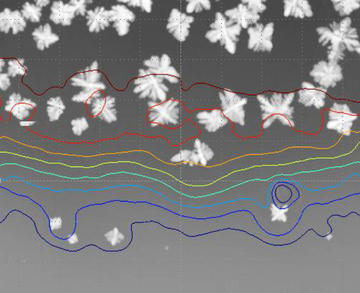
We describe an X-ray radiographic study of the crystallization behaviour of liquid alloys using X-ray radiography and machine learning in Science Advances. Working with colleagues the Department of Engineering Science, we used machine learning techniques to teach a computer to automatically detect the nucleation of crystals in terra-bytes of X-ray radiographic videos obtained during solidification experiments at the European Synchrotron Radiation Facility (ESRF). The quality of the videos combined with computer vision techniques allows the alloy composition at the point and instant of nucleation to be determined automatically, which in turn allows an estimate of the temperature and nucleation undercooling for every crystallization event. Studying thousands of nucleation events, we show how undercooling varies with solidification conditions, and explain how sudden bursts of crystallization are linked to the thermal-solute conditions in the liquid. Machine learning computer vision allowed enormous volumes of data that were unanalysable by hand to be converted robustly into distributions of nucleation undercoolings.